Why OEMs in the Process Equipment Industry Are Shifting to Managed Manufacturing Services for High-Quality & Compliant Production
In the fast-evolving world of manufacturing, supported by technology and government initiatives, outsourcing is becoming a strategic advantage for Original Equipment Manufacturers (OEMs).
You may be wondering why OEMs are making this shift. Well, it's not just a random choice – it’s a strategic decision with numerous benefits.
Let's dive into how outsourcing manufacturing services is proving to be a game-changer and a key catalyst for success.
We'll begin by looking at the challenges of in-house manufacturing and why many OEMs are moving away from it.
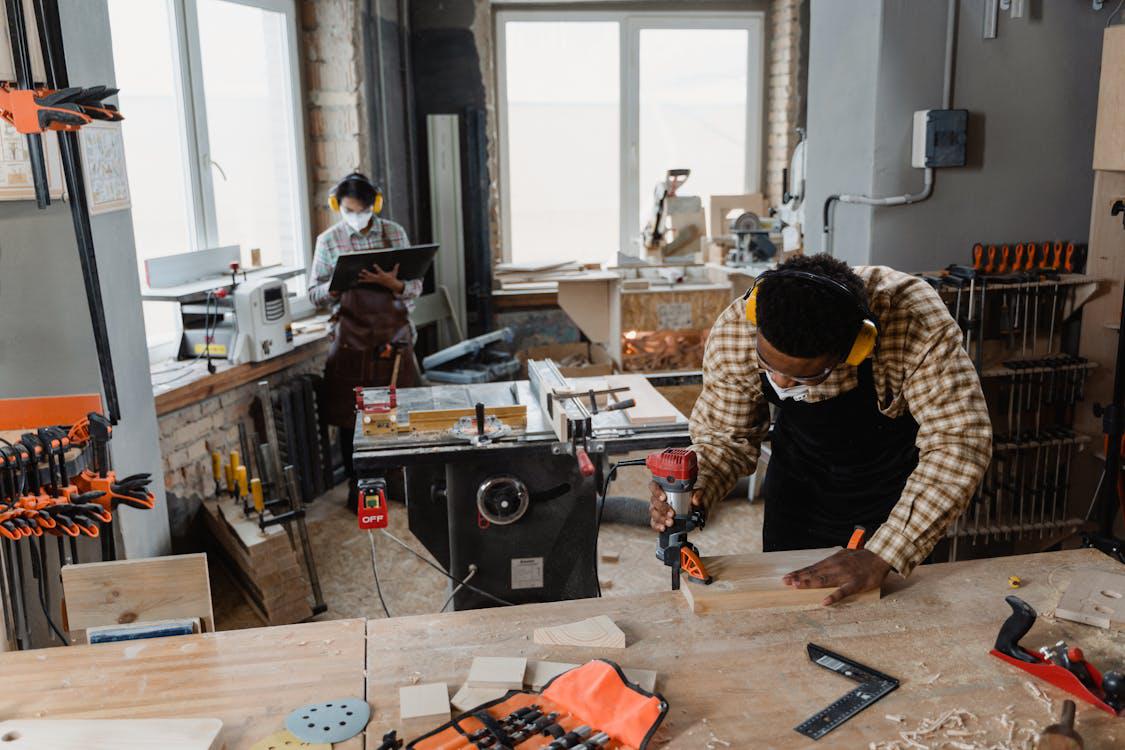
Challenges in In-House Manufacturing – High Capital Investment, Workforce Management, and Compliance Complexities Faced by OEMs
While things might look smooth from a distance, the reality of in-house manufacturing comes with a set of challenges that push OEMs to explore better options. Here are some of the key obstacles faced by OEMs in-house:
High Capital Investment:
For any organization, whether small or well-established, the goal is to maximize profits while minimizing costs. This objective is a major driving force behind the decision to outsource manufacturing. By working with contract manufacturers, OEMs benefit from economies of scale, enabling them to produce equipment more cost-effectively. This approach eliminates the need for significant investments in specialized machinery and facilities, allowing OEMs to allocate resources to areas that drive innovation and market expansion.Workforce Management:
Managing a large workforce while focusing on core tasks is both complex and exhausting. This is another reason OEMs are turning to managed manufacturing services. From workforce safety to inventory management, everything is handled by experts. This enables OEMs to shift their attention to creating strategies that increase revenue rather than getting bogged down in day-to-day operations.Compliance Complexities:
Navigating the maze of regulatory compliance can be particularly challenging in industries such as healthcare and medical devices. Contract manufacturers are well-versed in the ever-changing regulatory landscape, ensuring that products meet the required standards. By partnering with these manufacturers, OEMs gain confidence that their products will be produced in compliance with stringent industry regulations, reducing the risk of non-compliance issues.How Managed Manufacturing Ensures Cost Optimization – Reducing Overhead Costs, Material Waste, and Production Inefficiencies
After exploring the challenges involved, let's delve into how managed manufacturing services can benefit OEMs in the process equipment industry by ensuring cost optimization:
Reducing overhead costs
: Overhead costs are often the silent drain on a manufacturing business's profitability. While they are essential to keeping operations running, these indirect costs can quickly diminish profit margins if not properly managed. Managed services focus on reducing these costs to boost profitability and sustain competitiveness in the market. Here are a few strategies used to achieve this:- Implementing Technology and Automation
- Enhancing Energy Efficiency
- Cross-Training Employees
Material waste
: Managed manufacturing ensures minimal material waste by utilizing strategies like Just-In-Time (JIT) production, optimized inventory management, process monitoring, quality control, and continuous improvement initiatives. These strategies help produce only what is needed when it is needed, thus reducing overproduction and unnecessary material usage. The result is a substantial reduction in waste across the entire manufacturing process.Addressing Production Inefficiencies
: Managed manufacturing services focus on eliminating inefficiencies in the production process. By implementing a systematic approach to monitor and optimize all production aspects, such as identifying bottlenecks, reducing waste, optimizing resource allocation, improving workflows, and relying on data-driven decision-making, managed manufacturing significantly improves productivity. This leads to not only higher production capacity but also reduced operational costs.
Quality Assurance in Process Equipment Production – Meeting Stringent Industry Standards (ASME, API, PED, ISO) Through Controlled Manufacturing Processes
One of the major benefits of managed production services is they align the entire process with stringent global industry standards, such as:
- ASME (American Society of Mechanical Engineers) – Ensures structural safety for pressure vessels.
- API (American Petroleum Institute) – Mandates quality standards for oil & gas equipment.
- PED (Pressure Equipment Directive – Europe) – Ensures compliance for pressure-retaining parts in European markets.
Precision Fabrication for Critical Equipment – Importance of High-Quality Welding, Machining, and Finishing for Pressure Vessels, Heat Exchangers, and Reactors
In the process equipment industry, components like pressure vessels, heat exchangers, and reactors operate under extreme conditions—high pressure, temperature fluctuations, and corrosive environments. Precision fabrication ensures these critical assets meet safety, durability, and performance standards. Here's why high-quality welding, machining, and finishing are essential:
High-Quality Welding for Structural Integrity
Why It Matters:- Pressure vessels, heat exchangers, and reactors require leak-proof, high-strength welds to withstand high pressures and prevent failures.
- Poor welding can lead to cracks, leaks, and catastrophic failures, endangering workers and operations.
- Advanced Welding Techniques – Use of GTAW (TIG), SMAW (Stick), GMAW (MIG), SAW (Submerged Arc Welding) to ensure deep penetration and flawless seams.
- Non-Destructive Testing (NDT) – Techniques like radiographic (X-ray), ultrasonic, and dye penetrant testing to detect internal and surface defects.
- Certified Welders – Compliance with ASME Section IX, API 650, and PED standards ensures the highest quality welding processes.
Precision Machining for Dimensional Accuracy
Why It Matters:
- Components must fit exactly within specified tolerances to prevent operational inefficiencies or failures.
- Poor machining can cause misalignment, excessive vibration, and inefficiencies in heat transfer systems.
- CNC Machining – Automated 5-axis CNC machining achieves micron-level precision, ensuring uniformity in components.
- Tight Tolerances – Ensuring parts meet ±0.001 inches or better for critical applications.
- Specialized Cutting & Drilling – Plasma cutting, water jet cutting, and laser cutting deliver precision edges and minimal material distortion.
Superior Finishing for Corrosion Resistance & Longevity
Why It Matters:- Process equipment is exposed to corrosive chemicals, extreme temperatures, and pressure cycles.
- A poor surface finish can lead to premature wear, contamination risks, and efficiency loss.
- Polishing & Buffing – Electropolishing and mechanical polishing improve surface smoothness, reducing material buildup and corrosion.
- Protective Coatings – Thermal sprays, epoxy coatings, and PTFE coatings enhance chemical resistance.
- Shot Peening & Passivation – Increases fatigue resistance and prevents rust formation in stainless steel components.
Eliminating Compliance Risks with Certified Partners – How Managed Manufacturing Ensures Adherence to Global Regulatory Standards
With the growing number of regulations in recent years, regulatory compliance has become a critical focus for manufacturing companies. This has led to the creation of specialized compliance roles, such as quality assurance managers, regulatory affairs specialists, and compliance officers. Instead of hiring and managing multiple individuals to oversee compliance, which can be overwhelming, managed manufacturing services have emerged as a solution. These professionals are experts in ensuring that organizations meet strict legal mandates and relevant laws concerning product quality and safety.
Regulatory compliance processes provide vital guidance for manufacturers striving to produce safe, high-quality products while simultaneously achieving their business goals. Compliance is not just about meeting legal requirements—it also offers several strategic advantages:
- Demonstrating Commitment to Quality and Safety
- Building Trust with Customers and Stakeholders
- Gaining a Competitive Advantage
- Avoiding Costly Recalls and Legal Issues
For instance, ISO 9001 certification is a globally recognized standard that proves a manufacturer's commitment to quality management. Being transparent about compliance processes not only builds trust but can also enhance profitability and expand market share, giving the manufacturer a distinct competitive advantage.
Access to Specialized Manufacturing Expertise – Utilizing the Skills and Experience of Dedicated Fabrication Units for High-Performance Equipment
Manufacturing is not a walk into the park or something that anyone can do. It requires intense knowledge, skills, and years of experience to understand the complications of the process.
And outsourcing manufacturing services means skilled and dedicated fabrication experts for high-performance equipment.
How?
They use Advanced Fabrication Technology
Dedicated manufacturing units invest in cutting-edge technology that may be too costly for OEMs to maintain in-house, such as:
- CNC machining for precision components
- Automated welding for consistent quality
- Non-destructive testing (NDT) for defect-free production
- 3D modeling and simulations for design validation
This ensures that every component meets exact specifications and industry standards.
Experience with Critical Equipment Fabrication
Process equipment like pressure vessels, heat exchangers, and reactors requires expert craftsmanship and adherence to stringent regulations. Specialized manufacturers have proven experience in:
- Welding techniques like GTAW, SMAW, and SAW for high-strength joins
- Precision machining to achieve exact tolerances
- Surface treatments to enhance corrosion resistance and longevity
By outsourcing, OEMs gain access to decades of fabrication expertise without the burden of in-house training and equipment investment.
Supply Chain & Vendor Management Benefits – Ensuring Reliable Raw Material Sourcing and Reducing Dependency on Multiple Suppliers
An efficient supply chain guarantees access to dependable sources of raw materials, which helps minimize reliance on a single supplier. By diversifying the supplier base, companies can safeguard against any disruptions that could potentially halt production or delay timelines.
Vendor management plays a vital role in overseeing and optimizing the relationships between a company and its suppliers. It involves multiple steps, such as selecting and onboarding new vendors, negotiating favorable contracts, managing ongoing performance, and ensuring strict compliance with agreements. This process isn't just about finding suppliers, it's about creating strong, sustainable partnerships that benefit both parties.
For finance teams, managing these vendor relationships is critical for three primary reasons:
- Cost Control
- Quality Assurance
- Risk Reduction
Ensuring Consistency & Repeatability in Production – How Managed Services Maintain Uniform Quality Across Multiple Production Runs
Managed services depend on their client for business, and if they don’t deliver quality their business will shut in no time. Considering this, managed services maintain uniform quality across multiple production runs. Below is how they ensure this:
Standardized Processes & Protocols
: MSPs implement well-documented standard operating procedures (SOPs) to ensure every production run follows the same guidelines.Automation & Technology Integration
: Using automation tools, AI-driven monitoring, and cloud-based systems, MSPs reduce human errors and ensure precision in every production cycle. Automated quality checks detect inconsistencies early, preventing defects.Continuous Monitoring & Quality Control
: Managed services use real-time data tracking, IoT sensors, and performance analytics to monitor production quality. Any deviations from pre-set quality standards are flagged and corrected instantly.Skilled Workforce & Training Programs
: To ensure consistency, the working team must be updated with compliance and technology. MSPs invest in continuous employee training, keeping teams updated on industry standards and best practices for maintaining quality.Supplier & Material Consistency
: Uniform quality begins with consistent raw materials. MSPs establish long-term relationships with reliable local suppliers, ensuring quality raw materials reach them in a timely manner. Each production run starts with the same quality inputs.
Reducing Lead Times for Faster Market Deployment – Streamlined Processes That Help OEMs Meet Project Deadlines Without Delays
By having specialized teams with advanced skills and expertise, OEMs can ensure quicker turnarounds and improved efficiency. Here's how:
Prioritize Domestic Suppliers:
By focusing on reliable domestic suppliers, OEMs can reduce transit times, avoid customs delays, and strengthen local supply chain resilience.Increase Order Frequency:
By adjusting order frequencies and placing more frequent but smaller orders, businesses can maintain a steady supply of materials, reducing the chances of stockouts and production halts.Eliminate Unreliable Suppliers:
Cutting out unreliable suppliers ensures that only the most dependable sources are part of the supply chain, improving consistency and performance.Insulate Production Processes to Mitigate Unexpected Delays:
By implementing contingency strategies and streamlining production processes, companies can reduce vulnerabilities to unforeseen delays, ensuring smooth operations.Identify Bottlenecks, Rework, and Other Inefficiencies:
Identifying and addressing bottlenecks, rework, or inefficiencies in the system ensures faster production and fewer interruptions.
The Competitive Advantage of Outsourcing in Process Equipment Manufacturing – How OEMs can Focus on R&D, Innovation, and Customer Service While a Trusted Partner Handles Production
From the above, you may have a clear idea of the advantages of outsourcing in process equipment manufacturing. From reduced overhead costs to reduced waste production and increased profits, businesses have a lot to gain and nothing to lose.
Giving the manufacturing work to managed service providers, OEMs can focus on R&D innovations and divert their professionals to focus on what they do best – design, engineering, testing, marketing, etc. – and the crucial tasks that drive your company's success. For instance, reduced labor costs, Seamless scaling up or down, reduced equipment costs, and Streamlined processes.
When it comes to managing production series, India has maintained the momentum in the race to showcase its strength in process equipment manufacturing and become the priority option.
How?
The cost related to high-quality manufacturing is way less than that of any other nation.
It is not just the cost that is the reason behind India's growing reputation in the sector. The quality of the work and the dedication to meet international standards combined yield the products that the world appreciates.
For instance, Indian manufacturers supply ASME, API, and PED-certified equipment to global markets, reinforcing India's strength in precision engineering.
For more details on why the world is choosing India and how Refteck is playing its role in High-Quality Hand Tool Manufacturing,Click here.