Things to Consider for Efficient and Successful Spare Parts Management
Keeping a sizable inventory of spare parts on hand is something that many businesses avoid doing, mostly to keep operating expenses down. But if you also think the same way, it's time to reconsider your approach.
Effective spare part management is essential to maintaining seamless operations, including scheduled production halts and regular maintenance inspections. Inadequate spare part availability causes machinery to remain idle, which results in high expenses that might have been easily avoided with effective stock management.
To fully understand this subject's significance and how it will affect your business, let's take a closer look.
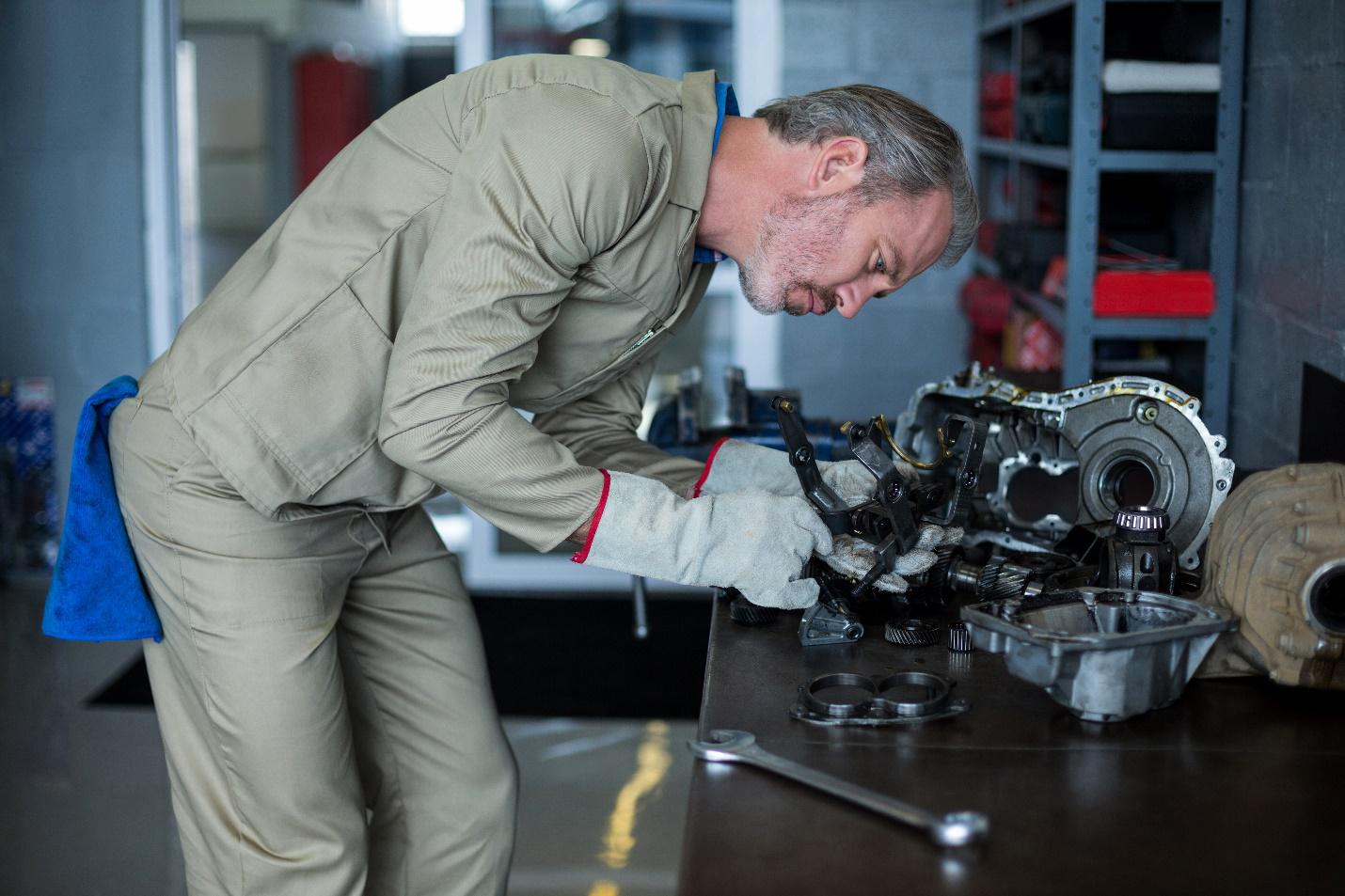
What Does Spare Parts Management Mean?
Spare parts management entails the strategic handling of components to ensure timely availability, adequate quantity, and optimal cost-to-quality ratio. It's about supplying the right parts to the right place at the right time.
Efficient management of spare parts plays a crucial role in equipment performance and maintenance costs. It encompasses various activities, from identifying and coding parts to acquisition, quality assessment, stocking policies, work planning, supplier management, and internal performance.
While many organisations understand the importance of spare parts management, some still overlook it to cut costs. However, maintaining a well-organised spare parts inventory can actually save both time and money in the long run. Hence, it's advisable to consider outsourcing spare parts management services for streamlined operations and cost-effectiveness.
Why is it Important?
Proper management of spare parts ensures that the equipment remains in good condition and operates smoothly.
This may cause your company to incur unforeseen costs and experience downtime.
That is why good spare parts management is critical to maintaining operations, regardless of the size of your gear or industrial setup. Let's examine in more detail the importance of spare parts management for companies of all sizes.
Avoid Unneeded Expenses :
When the production is running smoothly, businesses think purchasing spare parts may mean having to spend extra money at first. However, the scenario changes completely when equipment experiences failure, which later leads to efficiency loss, equipment downtime, and costly repairs. But do you know you can escape this unwanted situation?
Yes, by having the appropriate spare parts inventory level.
The amount of downtime will be low if you have the required spare parts on hand because they are already stocked. At the same time, constructing an effective spare parts management and planning system – 'll help businesses free up capital and reduce existing inventory while still maintaining high levels of accessibility and service.
Execute Roper Repairs :
What happens when tasks are rushed? Mistakes and delays are often the results. The same holds for machinery in production plants.
When machinery suddenly breaks down, managers often rush repairs to prevent major shutdowns. However, this hurried approach can lead to even costlier damage, especially if repairs are managed in-house or by calling a nearby mechanic.
To avoid such scenarios, it's crucial to establish an effective spare parts management system. This ensures that the right repairs are conducted at the right time. Additionally, engaging a trusted engineer to execute the repair or replacement process properly is essential for smooth operations.
Enhanced Safety :
Obsolete or failing parts can pose safety risks. Effective spare parts management ensures critical components are replaced before they become a safety hazard.
Improving Employee Productivity :
Quick access to necessary components is ensured by a well-managed spare parts inventory. Because employees can concentrate on their work more effectively and spend less time looking for or waiting on essential spare parts, overall productivity is increased.
Spare parts management is a systematic process that maximises resources, lowers expenses, and maintains seamless operations. It's essential for preserving equipment functionality, guaranteeing security, and eventually boosting a business's success.
Things to Consider for Effective Spare Part Management
Source of Stockout :
Identifying the root causes of stockouts to minimising their impact on your operations. While it's impossible to completely eradicate stockouts without investing in spare parts, understanding why they occur can help mitigate their effects.
Start by keeping real-time records of the reasons behind out-of-stock parts. This data will provide valuable insights into recurring issues and areas for improvement. Additionally, think about spending money on inventory management software to automate processes like monitoring inventory levels, establishing reorder points, and planning maintenance. This automation expedites the procedure as a whole and lowers the possibility of human error.
Identifying Critical Spares :
If the downtime doesn't have a major effect on your organisation, the spare parts required can be left out of a stocking plan.But if downtime has an impact on your profits, then it is important to take track of spare parts. Although, with hundreds of sites and thousands of spare part items, it's easy to see how some critical spares could be overlooked. That is why it is recommended to outsource the management service to experts who think about all the critical assets and systems you need replacement parts for thoroughly and maintain the inventory.
Assess Your Risk :
Equipment failures are inevitable, but taking a moment to gauge the risk of downtime can be a game-changer. It's all about making your life a whole lot simpler.
To assess risk, start by figuring out what one hour of downtime would cost your company. Once you have that, factor in lead times to determine the cost of an unexpected shutdown. Then, compare that to the expense of purchasing and storing replacement parts. Armed with this analysis, you can make informed decisions. Remember, even if the supplier has the part in stock, getting it to the site will still incur at least 24 hours of unscheduled downtime for the plant.
Building Strong Communication Between Internal Teams :
When it comes to spare parts management, your procurement and engineering teams must work in unison to determine which parts should be considered critical and accurately forecast their demand. While it is clear to see that having a well-stocked inventory of spares for critical assets minimises the risk of catastrophic failure, the reality is executing an effective management program is often more challenging than expected. Developing a strong partnership with your procurement team may be crucial in overcoming these challenges.
Summary :
With a clear understanding of the significance of spare parts management and the implementation of the outlined considerations, you have the opportunity to revolutionise your approach from reactive chaos to proactive efficiency.
For those without an in-house team to manage this critical process, consider outsourcing to the experts at Refteck for seamless and professional assistance.